Classification of high-pressure air compressor applications
What is a high-pressure air compressor?
High-pressure air compressors are used to compress air to pressures much greater than that of the atmosphere. This compressed air can then be used for a wide range of industrial and commercial applications, including powering pneumatic tools, filling scuba tanks and boosting fuel system pressures. Such compressors use a variety of technologies including reciprocating, rotary screw and centrifugal designs.
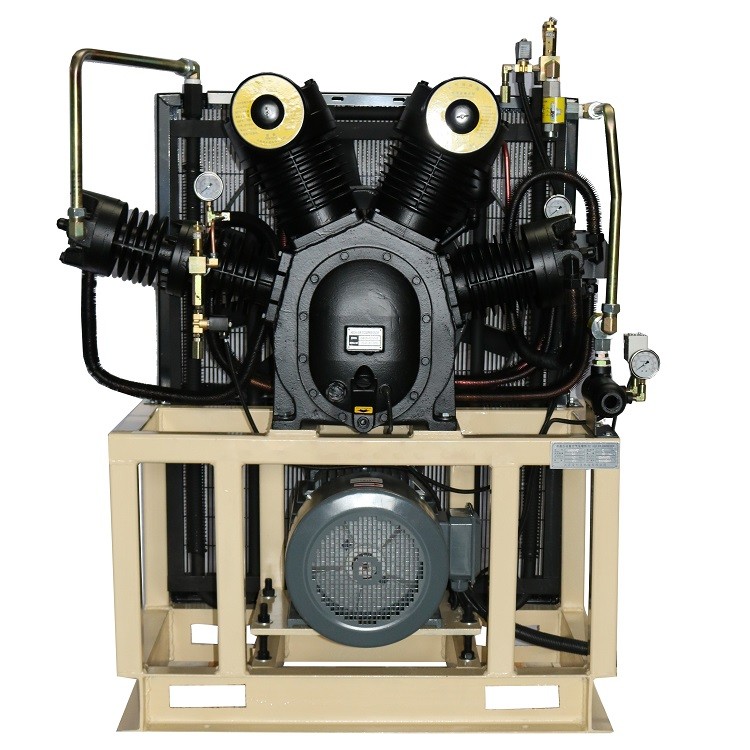
The main components of a high-pressure air compressor are:
The main components of a high-pressure air compressor are cylinders, pistons, rings, valves and connecting rods. The cylinders are the main part of the compressor, containing the intake and outlet valves that allow air to be drawn in and expelled. Inside the cylinders, pistons, typically driven by an electric motor, drive air compression. Compression is achieved using either air-ring valves or seal-ring valves. Rings are placed around the piston to ensure an airtight fit between the piston and the cylinder wall. Connecting rods connect the pistons to the crankshaft and rotate as the piston moves up and down in the cylinder.
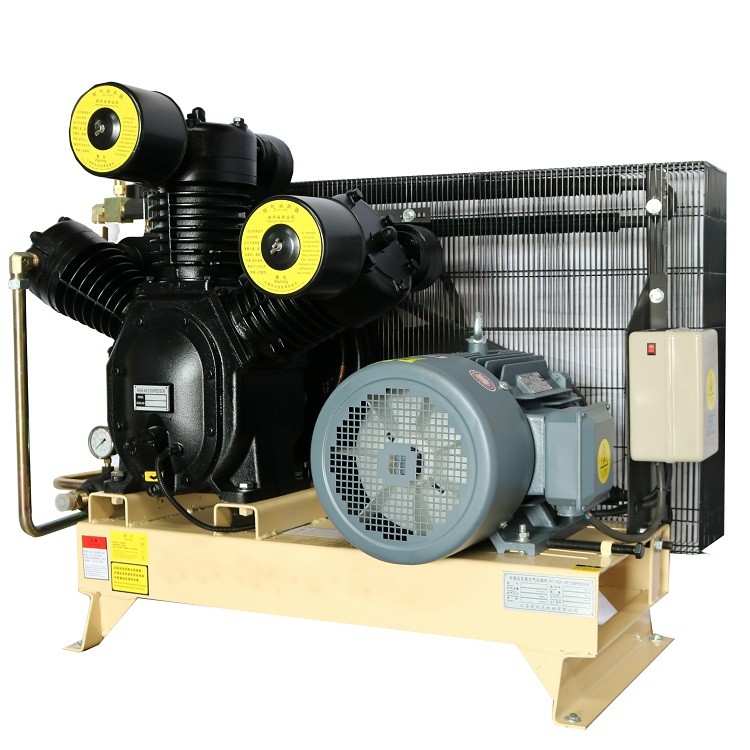
Application range of high pressure air compressor
Industrial applications
· Powering pneumatic tools
· Painting and spraying applications
· Production of food and beverages
· Manufacturing
· Construction
· Mining
· Oil and gas
· Agriculture
· Automotive applications
Powering air tools
· Tire inflation
· Brake bleeding
· Production of automotive parts
· Medical applications
Powering medical devices
· Production of medical equipment
· Recreational applications
Scuba diving
· Paintball
· Airgun shooting
· Production of recreational equipment
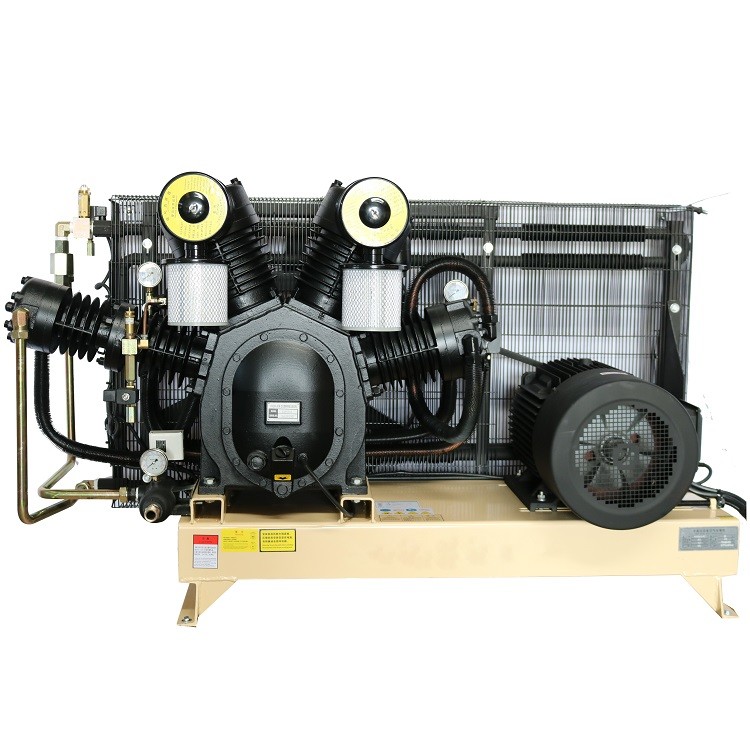
Precautions for the use of high-pressure air compressors
1. It is important to understand the technical requirements of the air compressor before use. Consult user manual and technical personnel in case of any difficulties.
2. Provide adequate ventilation while operating to prevent combustible gases and vapors from accumulating.
3. Make sure that the system is lubricated with the type and amount of oil recommended by the manufacturer.
4. Operate the equipment in a clean, dry, and well-ventilated environment. Avoid using in a dusty or wet area.
5. Do not modify the machine without the assistance of qualified personnel.
6. It is important to check for air leaks, broken hoses, or other signs of wear and tear regularly.
7. Avoid overloading the machine.
8. Shut off the device after every use.
9. Maintain all safety devices to ensure the safe operation of the machine.
10. All electrical equipment should be installed and maintained by electricians trained in the use of high voltage equipment.
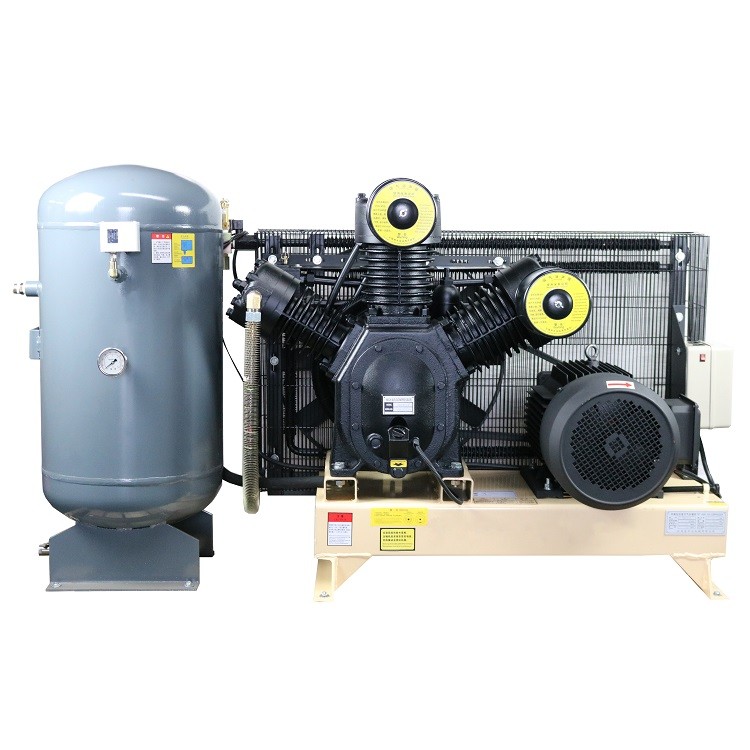
Precautions for maintenance of high pressure air compressor
1. Ensure the necessary safety protection devices (such as gas lines, pressure gauges, safety valves, etc.) are in good condition and working properly.
2. Always exhausted the air circuit before repairing or moving the compressor.
3. Check all the parts of the compressor including the motor, hoses and seals for any damage or wear.
4. Change the oil regularly as per the recommended levels and replace the air filters as needed.
5. Check for any leakage of air from the joints or valves; if leaking tighten the valves and fittings.
6. Regularly check the air pressure, oil pressure and temperature of the compressor.
7. Strictly follow the lubrication chart to ensure proper lubrication of the moving parts.
8. Clean the dirt and dust accumulation from the air chamber, motor and cooling fins regularly.
9. Make sure that the motor and other components are not exposed to high temperatures.
10. Always consult a professional for any major repairs or for troubleshooting any issue related to your air compressor.