How to Deal with Oil Leakage and Dripping in Air Compressors?
How to Deal with Oil Leakage and Dripping in Air Compressors?
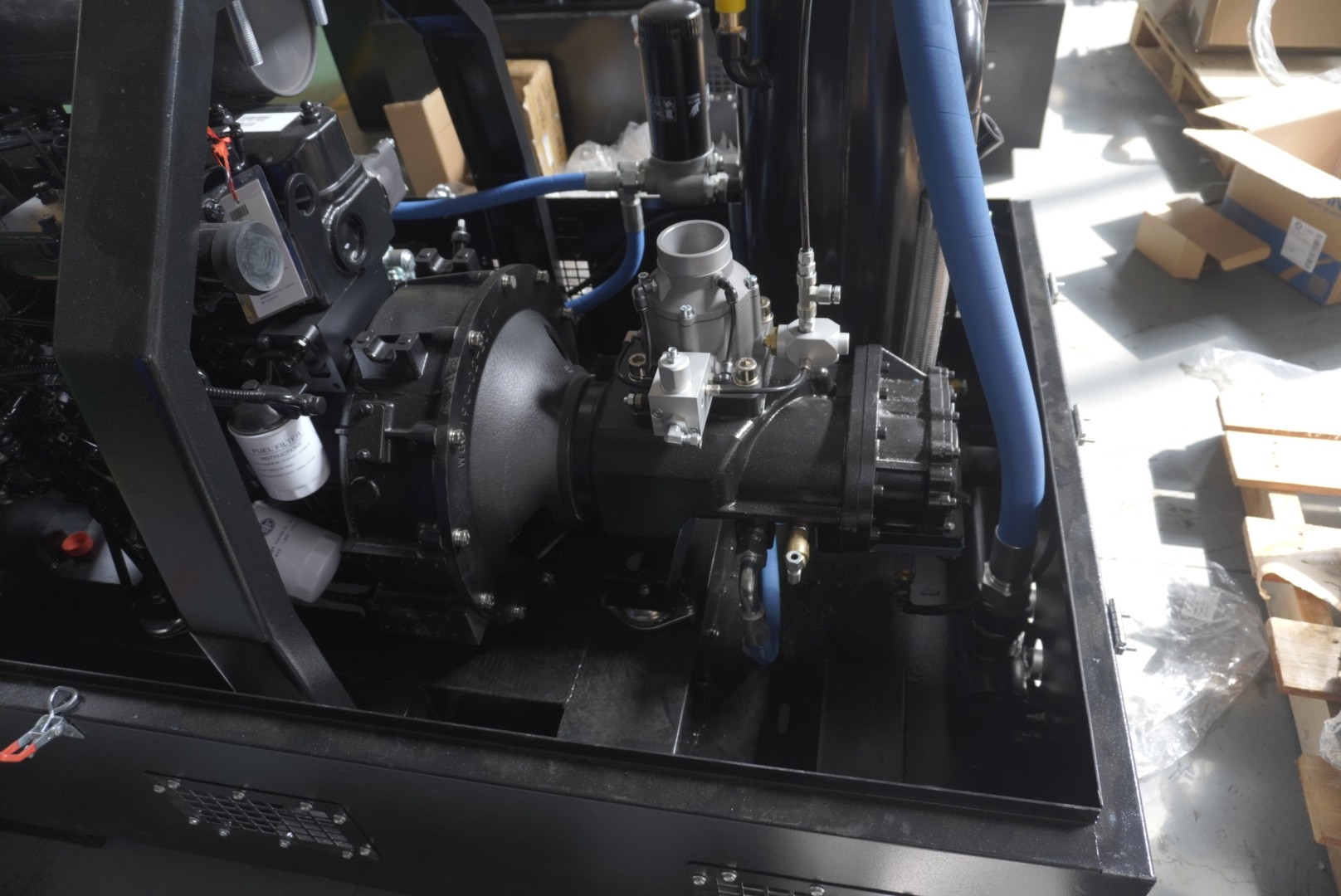
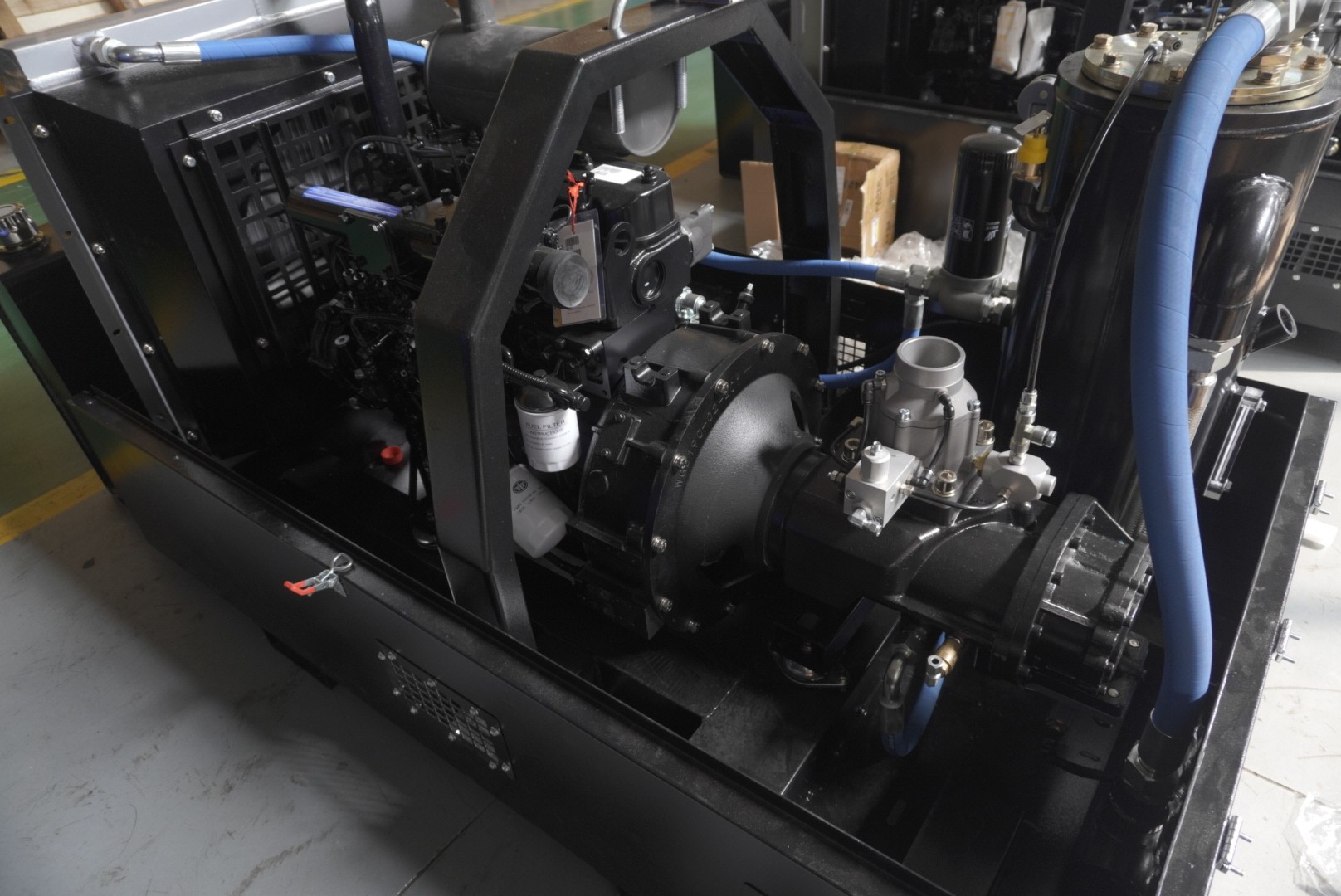
A tightly sealed air compressor oil system usually does not leak oil. However, if maintenance is not timely or unexpected situations occur during operation, oil leakage may still occur. Once an oil leak occurs, it may cause production suspension or greater losses to air compressor users, so we must understand how to deal with air compressor oil leakage.
According to the different oil leakage conditions, air compressor oil leakage can be divided into three types: oil seepage, oil leakage, and oil dripping.
1. Oil Seepage
Oil seepage is usually caused by loose connections. Under high pressure, the oil system will have tiny leaks in weak links. If it is discovered and repaired in time, it will not cause more serious failures. But if the oil seepage lasts too long, it may cause a disaster. In the event of oil seepage, the connection can be tightened in the shutdown state to solve the problem.
Oil seepage is a subtle issue that can often go unnoticed until it becomes a significant problem. The primary cause of oil seepage is loose connections within the air compressor system. These loose connections can occur at various points, such as joints, fittings, or seals. When the air compressor operates under high pressure, these weak links can develop tiny leaks, allowing oil to seep out slowly.
To address oil seepage effectively, it is crucial to conduct regular inspections of the air compressor system. During these inspections, pay close attention to all connection points and look for any signs of oil seepage. If oil seepage is detected, it is essential to take immediate action. The first step is to shut down the air compressor to prevent further oil loss and potential damage.
Once the air compressor is in a shutdown state, carefully inspect the affected connections. Tighten any loose fittings or joints to ensure a secure seal. In some cases, it may be necessary to replace worn-out seals or gaskets to prevent future oil seepage. By addressing oil seepage promptly, you can avoid more severe issues and maintain the efficiency of your air compressor system.
2. Oil Leakage
Oil leakage is usually caused by blockage of the oil cooler of the screw air compressor. Oil cooler blockage is a common fault of screw air compressors. The main reason is that there are impurities in the circulation system, which causes the thin copper tube of the oil cooler to be blocked, so that the oil cannot pass through the oil cooler, resulting in oil leakage. The main way to deal with this fault is to dredge the oil cooler. The specific method is to first take out the oil cooler core, add a descaling agent to soak it, and then use a soft copper wire to dredge the scale inside the cooler core one by one.
Oil leakage is a more severe issue compared to oil seepage and requires immediate attention. The primary cause of oil leakage in screw air compressors is the blockage of the oil cooler. The oil cooler plays a crucial role in maintaining the temperature of the oil within the compressor system. When the oil cooler becomes blocked, it can no longer effectively cool the oil, leading to oil leakage.
The blockage of the oil cooler is often caused by impurities present in the circulation system. These impurities can accumulate over time and obstruct the thin copper tubes within the oil cooler. As a result, the oil cannot flow through the cooler, causing pressure to build up and leading to oil leakage.
To address oil leakage caused by a blocked oil cooler, follow these steps:
1. Shutdown the Air Compressor: Before performing any maintenance, ensure that the air compressor is in a shutdown state to prevent accidents and further damage.
2. Remove the Oil Cooler Core: Carefully take out the oil cooler core from the compressor system. This core contains the copper tubes that need to be cleaned.
3. Soak in Descaling Agent: Prepare a descaling agent solution and soak the oil cooler core in it. The descaling agent will help dissolve and loosen the scale and impurities inside the copper tubes.
4. Dredge with Soft Copper Wire: After soaking, use a soft copper wire to gently dredge the inside of each copper tube. This process will remove any remaining scale and ensure that the tubes are clear and unobstructed.
5. Reassemble and Test: Once the oil cooler core is thoroughly cleaned, reassemble it into the compressor system. Conduct a test run to ensure that the oil cooler is functioning correctly and that there are no more oil leaks.
Regular maintenance and cleaning of the oil cooler are essential to prevent oil leakage and ensure the efficient operation of the air compressor.
3. Oil Dripping
Oil dripping is often not easy to find in time. It is generally caused by loose connection parts or increased pressure. The way to deal with oil dripping is basically the same as oil leakage. You can refer to the oil leakage treatment method. However, if there are deep-seated reasons, you must eliminate the hidden dangers before handling.
Oil dripping is a common issue that can be challenging to detect in its early stages. It typically occurs due to loose connection parts or increased pressure within the air compressor system. While oil dripping may seem less severe than oil leakage, it can still lead to significant problems if left unaddressed.
To deal with oil dripping effectively, follow these steps:
Inspect for Loose Connections: Regularly inspect all connection points within the air compressor system. Look for any signs of oil dripping and identify the source of the issue. Tighten any loose fittings or joints to prevent further oil loss.
Check for Increased Pressure: Monitor the pressure levels within the air compressor system. Increased pressure can exacerbate oil dripping. Ensure that the pressure is within the recommended range and make any necessary adjustments.
Refer to Oil Leakage Treatment: The treatment method for oil dripping is similar to that of oil leakage. If the oil dripping is caused by a blocked oil cooler, follow the steps outlined in the oil leakage section to clean and maintain the oil cooler.
Eliminate Hidden Dangers: If there are deep-seated reasons for oil dripping, such as worn-out seals or damaged components, address these issues before proceeding with repairs. Replace any faulty parts to ensure the long-term stability of the air compressor system.
In short, when dealing with oil leakage in screw air compressors, we should pay great attention. In addition to daily inspections, regular maintenance and maintenance should be carried out. At the same time, the oil cooler core should be cleaned regularly, and spare parts should be prepared to ensure the normal operation of the screw air compressor.
By following these guidelines and conducting regular maintenance, you can effectively manage oil seepage, oil leakage, and oil dripping in your air compressor system. Proper care and attention will help prevent production disruptions and ensure the efficient operation of your equipment.