How to reduce energy loss from an air compressor?
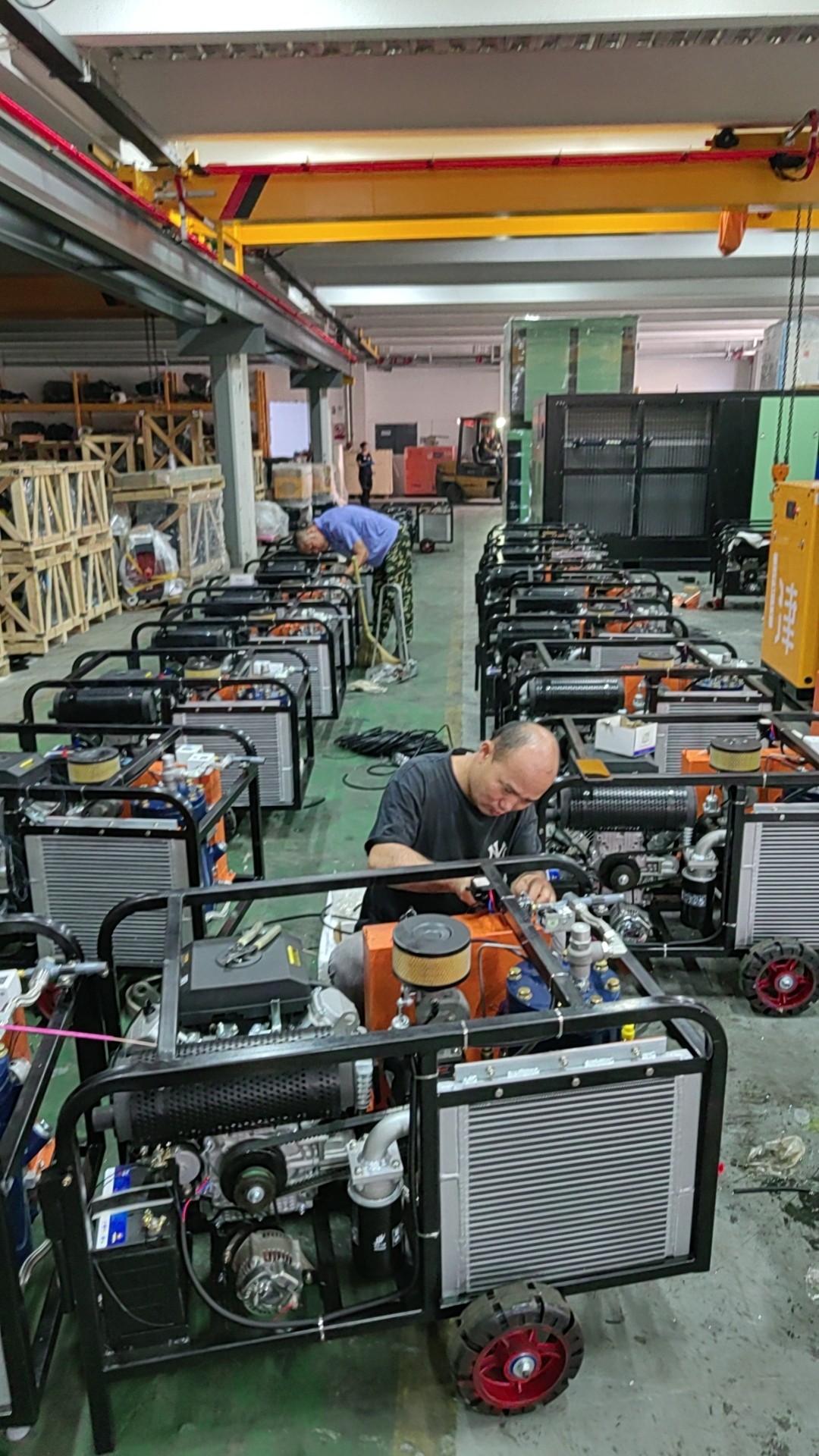
Air compressors are essential tools in many industrial and commercial operations, from manufacturing plants to automotive shops. Unfortunately, however, air compressors can also be one of the largest energy consumers within these environments - often accounting for as much as 30% of overall usage costs in one facility! With such high energy costs associated with operating air compressors comes an imperative need to find ways to minimize energy losses and maximize efficiency - using best practices and strategies businesses can significantly decrease their energy consumption, lower operating costs, and decrease their environmental footprint.
Understand Air Compressor Energy Losses
Prior to embarking on strategies designed to reduce energy loss in an air compressor system, it's crucial that one fully comprehends where and why energy loss occurs. Some key sources include:
1. Leaks: Air leaks are among the primary sources of energy loss in compressed air systems, leading to significant energy waste from even small leaks accumulating over time and leading to significant inefficiency.
2. Pressure Drops: Pressure drops occur when there is an unexpected loss of pressure when compressed air moves through pipes, filters, dryers and other components of an HVAC system. Excessive pressure drops require more work from a compressor in order to maintain desired levels, driving up energy usage.
3. Improper Compressor Sizing: Selecting an improper compressor size can result in inefficiency, as an over- or undersized compressor may consume too much energy for its intended application; conversely, an undersized one could struggle to meet demands, leading to prolonged operation and unnecessary energy waste.
4. Poor Maintenance: Poor maintenance practices can lead to clogged filters, worn-out parts and inefficient operation - all factors which contribute to increased energy usage.
5. Inefficient Controls and Start/Stop Cycles: Continuous compressor operation or outdated control systems can waste energy. Managing start/stop cycles efficiently and installing advanced control systems can help maximize energy usage.
6. Heat Loss: Air compressors generate large amounts of heat during operation, much of which goes unused without proper heat recovery systems in place. Recovering and using this energy can significantly improve system efficiency.
7. Misuse of Compressed Air: Sometimes compressed air is overused to perform tasks that could be completed more efficiently with other approaches. By knowing when and why to utilize compressed air versus using alternative solutions can help reduce energy usage, energy bills may be significantly decreased.
Strategies to Minimize Energy Loss in Air Compressor Systems
To address energy loss from air compressors, it's critical to adopt an holistic strategy which includes system design, maintenance and operational practices. Here are some effective strategies for minimizing energy loss:
1. Conduct Regular Leak Detection and Repair
Air leaks are one of the primary sources of energy loss in compressed air systems. According to the U.S. Department of Energy, even one 1/8-inch leak can cost an institution as much as $2,500 annually in wasted energy costs; so regular leak detection and repair procedures must be conducted in order to minimize energy wastage.
Ultrasonic Leak Detectors**: Ultrasonic leak detectors are an invaluable way of quickly and accurately pinpointing air leaks that may not be apparent to the naked eye. By regularly inspecting your compressed air system - including pipes, fittings, valves and fittings - with this detector in hand, pinpointed leaks can be more quickly located and repaired.
Implement a Leak Prevention Program**: Develop and implement a leak prevention program with regular inspections, employee training sessions and maintenance schedules in place to detect and repair leaks as soon as they arise.
2. Optimize System Pressures
Operating at higher pressure than necessary leads to higher energy usage; each 2 psi increase in pressure results in an estimated one percent increase in energy use. To optimize system pressure:
Adjust for Lowest Effective Pressure**: Determine the minimum pressure necessary for your application and set your system accordingly, as reducing pressure can yield considerable energy savings.
- *Utilize Pressure Regulators and Stabilizers*: Install pressure regulators at points of use to ensure the pressure doesn't exceed necessary limits, while pressure stabilizers help ensure consistent levels throughout your system.
Avoid Artificial Demand**: Artificial demand occurs when operating at higher pressure than required, resulting in excessive air consumption. Reducing pressure to its required level eliminates artificial demand and lowers energy loss.
3. Make Sure That the Right Compressor Size Is Acknowleged
Selecting an appropriately sized compressor for your application is paramount in order to avoid energy losses and boost performance. An over or undersized compressor could result in inefficiencies.
Conduct a Demand Analysis**: Analyse the air demand of your operations to select an appropriate compressor size, including peak demand periods and base load requirements when selecting one.
Use Variable Speed Drive (VSD) Compressors**: VSD compressors can adapt their output based on demand, saving energy during periods of low demand while maximizing efficiency regardless of fluctuating usage patterns. This type of flexibility ensures the compressor always operates at maximum efficiency regardless of fluctuations.
4. Implement Effective Control Systems.
Advanced control systems can significantly increase the energy efficiency of air compressors, by preventing unnecessarily long runs and optimizing their operation.
- Apply Centralized Control Systems**: For facilities with multiple compressors, using centralized control systems can help coordinate their use to ensure only necessary units are running at once and prevent excess energy use due to running multiple compressors at once. This reduces excess consumption from running multiple compressors simultaneously.
Implement Start/Stop Controls**: Installing start/stop controls allows compressors to shut off during periods of low demand, saving energy while avoiding running idle and wasting precious resources.
Utilize Load/Unload Controls**: Load/unload controls enable compressors to operate at full capacity when required and reduce energy waste during periods when demand drops off, saving energy during idle times.
5. Regular Maintenance and Monitoring
Regular maintenance is key to ensure air compressors run at peak performance, without which components could degrade and lead to increased energy usage.
- Replace Air Filters Regularly**: Clogged or dirty air filters restrict airflow, increasing pressure drop and forcing compressors to work harder. Regularly replace or clean filters in order to achieve optimal airflow and efficiency.
- *Inspect and Replace Worn-Out Parts*: Worn-out seals, valves, and bearings can lead to air leakage and reduce compressor efficiency, so regular inspections and timely replacement help maintain compressor performance.
Monitor Performance Metrics**: Implement monitoring systems to keep an eye on key performance indicators (KPIs), such as pressure, temperature and power usage. Analyzing this data can help pinpoint inefficiencies and prompt corrective actions to be taken immediately.
6. Recover and Utilize Waste Heat
Air compressors produce significant heat during operation, and can convert up to 90% of their electrical energy consumption into heat. Without heat recovery systems in place, this energy would simply go to waste; by employing heat recovery solutions you can capture and reuse it for other uses while also reducing overall energy consumption.
Install Heat Recovery Systems**: Utilizing heat exchangers to capture waste heat from compressor cooling systems can result in considerable energy savings when used for space or water heating or industrial processes, providing significant cost-cutting potential.
Integrate Heat Recovery Systems into Existing Systems**: For optimal energy efficiency, consider integrating heat recovery systems with existing HVAC and process heating systems in your facility to increase energy savings.
7. Optimize Piping and Distribution Systems
Poorly planned piping and distribution systems can lead to pressure drops and energy waste, leading to pressure decrease and ultimately wasteful expenditure of energy. To optimize piping and distribution:
- Sizing Your Pipes Accurately: For maximum pressure drop and efficiency, ensure your piping is the appropriate size to reduce pressure drops. Oversized or undersized pipes may create resistance and create inefficiency, leading to inefficiencies in operation.
- Minimize Bends and Fittings: Excessive bends, fittings, and connections can lead to frictional losses and pressure losses in your pipe layout, so aim to limit their presence to reduce pressure drops.
-Install Looped or Ring Piping Systems: Looped piping systems provide multiple paths for compressed air distribution, helping reduce pressure drops while increasing distribution efficiency.
8. Reduce Misuse of Compressed Air
Compressed air is often misused for applications that could be accomplished more effectively using different techniques, and by decreasing unnecessary use it could help significantly lower energy consumption and therefore save on energy costs.
Identify Non-Essential Uses: It is important to identify non-essential uses for compressed air such as cleaning or cooling and replace these activities with energy-saving alternatives such as electric blowers or vacuums, so as to maximize energy efficiency.
Train Employees: Make employees aware of the costs associated with compressed air usage and encourage them to only use it when necessary - this will reduce unnecessary air consumption and energy waste.
9. Implement Energy Efficient Accessories
Accessories such as dryers, filters and separators play a critical role in maintaining the quality of compressed air but they may also contribute to energy loss if they're not managed effectively.
Use Energy-Efficient Air Dryers: Desiccant dryers and refrigerated dryers are widely used to extract moisture from compressed air, while cycling dryers that adjust based on demand may also help. Select energy-efficient models when shopping for desiccant or refrigerated dryers.
Optimize Filters and Separators: High-efficiency filters and separators can significantly reduce pressure drops and energy usage, helping you save both money and resources. Regular maintenance of these accessories will ensure their optimal performance.
10. Conduct Routine Energy Audits
Regular energy audits can help identify areas in which energy is being wasted and suggest opportunities for optimization of efficiency in compressed air systems. An energy audit provides a thorough evaluation of your compressed air system's performance as well as suggestions to increase its efficacy.
Hire Professionals**: For a comprehensive assessment of your compressed air system, consider consulting with an energy auditor who can offer invaluable insight and suggest specific measures to mitigate energy waste. They could provide invaluable guidance as well as provide invaluable recommendations that could lead to energy savings.
Implement Recommendations**: After conducting an audit, implement any recommended changes to increase your compressed air system's performance while decreasing energy usage.
Reducing energy loss from air compressors requires taking an integrated approach that involves regular maintenance, optimization of system components, effective control, employee awareness and more. Businesses that implement such strategies can realize significant energy savings, reduced operational costs and contributed towards creating a more sustainable environment. With such high energy costs associated with compressed air systems, even small improvements in efficiency can yield substantial financial rewards over time - so investing in energy-saving practices for air compressors should be seen as smart investments by any facility looking to optimize operations.
250 Bar High Pressure Air Compressor with Electric
ECO-friendly Adsorption Type Compressed Air Dryer for Compressor
Air Dryer Refrigerated Type Compressed Air Dryer for Compressor
Electric Driven Portable Screw Air Compressor for Drilling Rig