How is loading and unloading done in screw compressors?
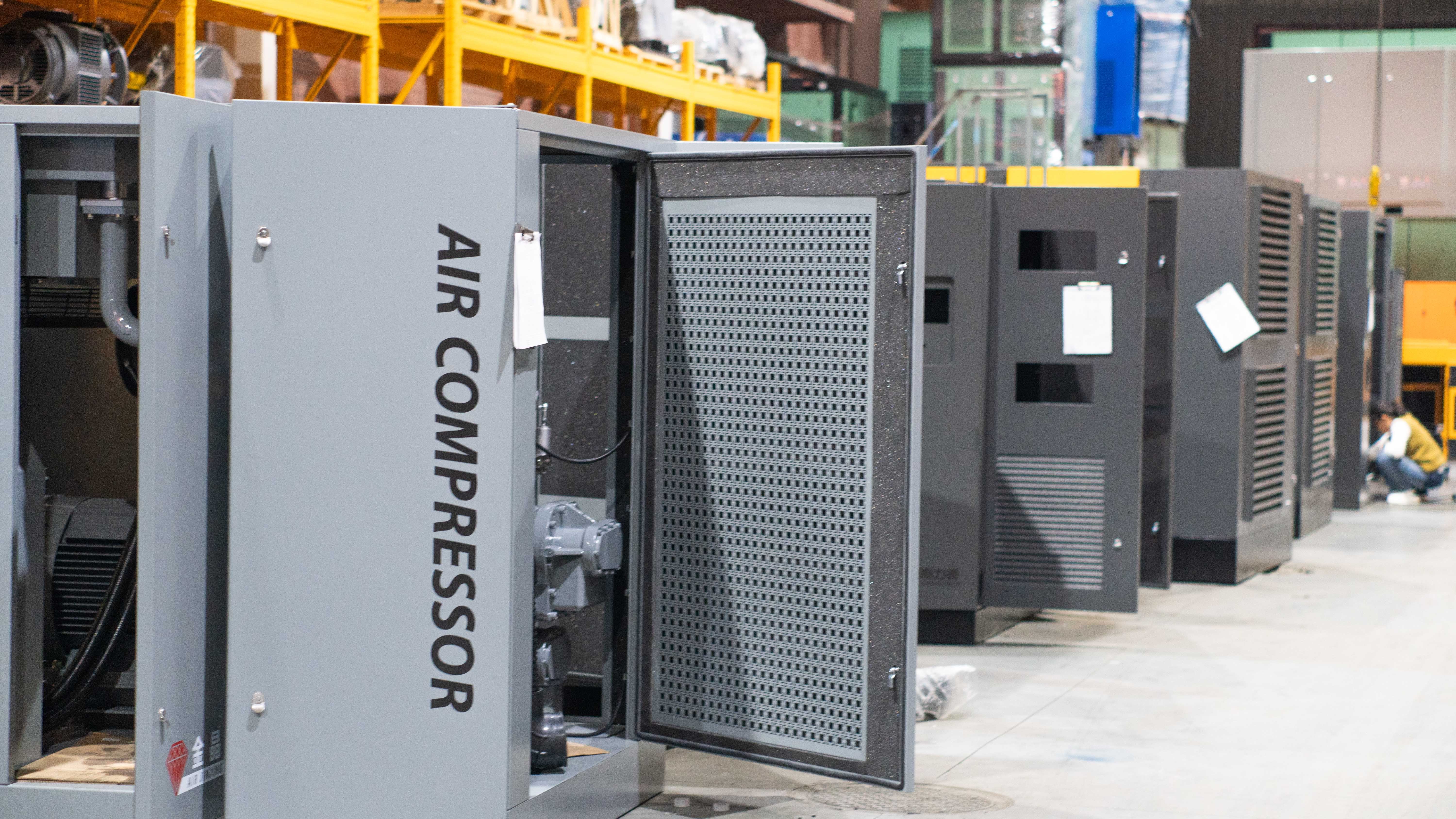
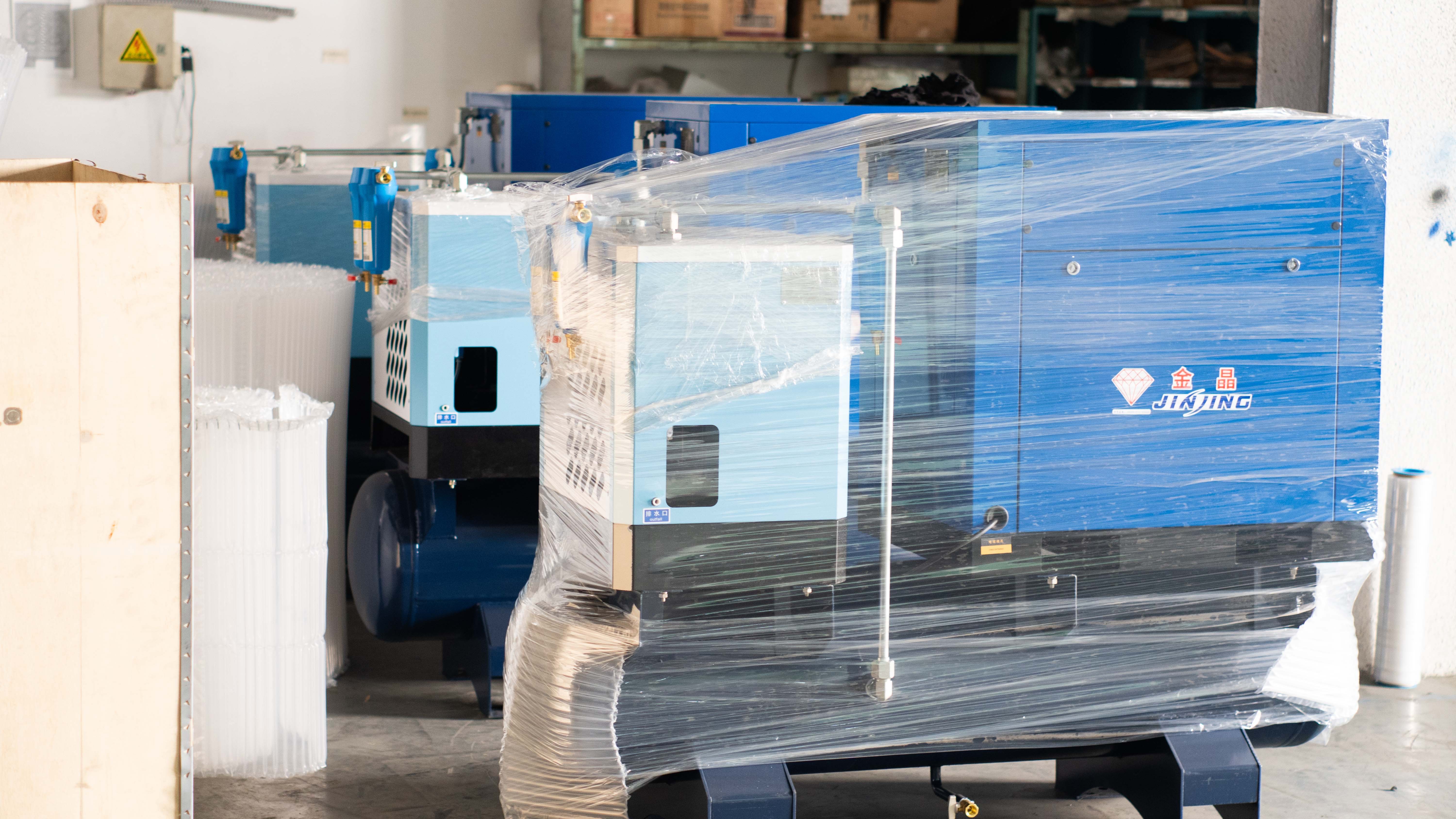
Screw compressors are integral parts of many industrial applications due to their efficiency, reliability, and ability to continuously provide compressed air. Loading and unloading processes in these compressors play a pivotal role in their operations - impacting energy consumption, pressure regulation, system efficiency and system energy consumption. This comprehensive guide covers their working principle as well as mechanics of loading/unloading operations as well as automatic controls' impact on efficiency as well as common issues and solutions related to them.
1. Introduction of Screw Compressors
Working Principle of Screw Compressors
Screw compressors, commonly referred to as **rotary screw compressors**, operate on the principle of positive displacement. They use two meshing helical rotors (screws) with meshing helical rotors (screws) interlocked by gears (or cogs) and their screws rotating in tandem with each other to compress air or gas by trapping it between their rotating blades thereby decreasing volume and increasing pressure - unlike reciprocating compressors which deliver compressed air pulse by pulses.
This operation can be divided into three distinct phases.
1. Suction Phase:
Air is drawn into the compressor through an intake valve, where its rotation creates a vacuum between each of its rotors allowing atmospheric air to fill these spaces between each of them and into the cavity between.
2. Compression Phase:
As the rotors continue turning, air becomes trapped between their lobes and is directed toward the discharge end, compressing and increasing in pressure as its volume decreases.
3. Discharge Phase:
At this stage, high-pressure compressed air is released through its discharge end either directly into a storage tank or directly into a pneumatic system.
Components of a Screw Compressor
A screw compressor consists of multiple components that work together for efficient compression:
- Air-End:
At the center of all compression activity lies two intermeshing helical rotors (male and female rotors).
Inlet Valve**: It regulates how much air enters into compression chamber.
- Oil Separator:
Oil-injected screw compressors require this component to separate oil from compressed air. Coolers help dissipate any heat generated during compression for optimal operating temperatures.
Pressure Sensors: Continuously monitor system pressure and provide feedback to the control system for adjusting loading/unloading cycles.
Control System: Oversees all operations associated with compressor operation such as starting, stopping, loading/unloading cycles etc.
1. Loading Process for Screw Compressors
Loading process** of a screw air compressor** involves actively compressing air before delivering it to the system, in order to guarantee consistent supply while still optimizing energy efficiency of the compressor.
Loading Valve Function
Screw compressor loading valves, more commonly referred to as intake valves, play an essential part in the loading process. Once the compressor has reached a "loaded" state, they open to allow air into the compression chamber for compression - this action directly determines how much compressed air output and system pressure there will be from compressed air output and system pressure measurement systems.
Steps Involved in Loading Process
1. Signal from Pressure Sensor: When the pressure sensor detects a decrease in system pressure below its predetermined threshold, it sends an indication to the control system to begin loading operations.
2. Opening of Loading Valve: Once activated by the control system, air enters the compression chamber through its loading valve.
3. Air Compression Rotors compress this air as it travels towards its discharge end to increase pressure and eventually discharge it at full pressure.
4. Releasing Compressed Air: Once compressed air has been released through its discharge port and delivered to either a system or storage tank, its pressure can be released through its outlet port and released as needed.
Changes in Pressure While Loading
As the compressor delivers compressed air to its system, its pressure gradually increases over time. A pressure sensor constantly monitors these fluctuations to ensure system pressure reaches the desired level.
Unloading Screw Compressors
Unloading of a screw compressor involves stopping air compression while keeping the compressor running in order to conserve energy and protect its components from premature wear and tear.
Function of Unloading Valve
A screw compressor unloading valve is designed to release pressure in its air-end once system pressure has reached desired levels, helping ensure system stability, prevent overheating and optimize energy use during idle periods.
### Steps in the Unloading Process
1. Detection of High Pressure:
Once a pressure sensor detects that system pressure has exceeded an upper threshold threshold, it notifies the control system immediately.
2. Activation of Unloading Valve:
When activated by the control system, this valve opens, releasing air trapped in the compressor's air-end and venting it out through vent pipes to lower internal pressure and return it to an unloaded state for efficient functioning of the compressor.
3. Idle Operation:
When not loading air into containers, the compressor runs without compressing air, maintaining readiness for switching on when required.
Pressure Changes When Unloading
As air is released from a compressor's interior pressure increases as trapped air escapes; system pressure remains relatively stable thanks to air stored in a receiver tank.
Automatic Control of Loading and Unloading
Screw compressors rely on automatic control systems to maximize their efficiency, using sensors and programmable logic controllers (PLCs) to regulate loading and unloading processes. These systems rely on real-time pressure readings from sensors to adjust compressor operations accordingly.
Benefits of Pressure Sensors
Pressure sensors are essential components of effective screw compressor pressure management. They monitor system pressure and relay this data back to the control system, which uses it to determine when to load or unload the compressor.
How the Control System Regulates Loading and Unloading
The control system utilizes sensors, solenoid valves and PLCs to automate loading and unloading:
1. Monitoring Pressure Levels:
Pressure sensors continuously measure system pressure levels and relay this information back to the PLC for analysis.
2. Triggering Valve Operations:
Based on pressure readings, the PLC determines when to open or close loading and unloading valves to maintain system pressure within an acceptable range.
3. Modulating Valve Actions:
The control system can adjust valve opening and closing actions in order to maintain pressure consistency while optimizing energy use, helping maintain efficiency by maintaining automatic adjustment of screw compressors.
4. The Effect of Loading and Unloading on Screw Compressor Efficiency
Loading and unloading cycles play a pivotal role in the efficiency of screw compressors, leading to significant energy savings and extended equipment life. By carefully managing these cycles, proper regulation may result in substantial energy cost reductions as well as extended equipment lifespan.
Energy Analysis Report
Frequent loading and unloading can increase energy usage due to repeated starting and stopping cycles of the compressor, thus leading to an increase in energy expenditure. Therefore, optimizing these cycles for energy efficiency optimization of screw compressors is of utmost importance in optimizing their energy performance.
Ways to Reduce Loading and Unloading Frequencies
1. Vary the Pressure Settings:
Altering pressure settings between loading and unloading points can reduce frequency of cycles and thus save energy.
2. Variable Speed Drives (VSDs):
Implementing VSD technology allows the compressor motor to adjust its speed depending on demand, eliminating the need for frequent loading and unloading of equipment.
3. Advanced Control Systems:
Implementing advanced control systems that anticipate air demand and adjust operations accordingly can significantly decrease energy loss while improving compressor efficiency.
4. Common Issues and Solutions for Maintenance Requirements
Even though screw compressors can be efficient, loading and unloading issues may arise that impede performance.
Causes and Solutions of Insufficient Loading
Cause and Solution for insufficient Loading*
Its Its mes Its mes Its mes - Cause: Inadequate Loading may result from either a malfunctioning screw compressor loading valve or incorrect pressure settings. For optimal loading results, inspect and replace as needed while making necessary changes in pressure settings to meet system needs.
Solutions to Incomplete Unloading Problems (and Why they Exist)
Cause: Incomplete unloading may be the result of a malfunctioning screw compressor unloading valve or blocked air pathways, with regular maintenance and inspection to keep such issues at bay. Solution: Clean or replace the unloading valve as soon as possible to clear all air pathways; cleaning can help prolong its effectiveness as a solution.
Understanding how loading and unloading processes in screw compressors are managed is vital to optimizing their performance and energy efficiency. By employing automatic controls, proper maintenance, and VSDs to regulate these processes, operators can achieve significant energy savings while prolonging equipment lifespans. Regular troubleshooting helps maintain optimal compressor efficiency and reduce downtime ensuring industrial operations run efficiently while remaining cost effective.