What type of compressor is most often used in large chillers?
What Type of Compressor Is Most Often Used in Large Chillers?
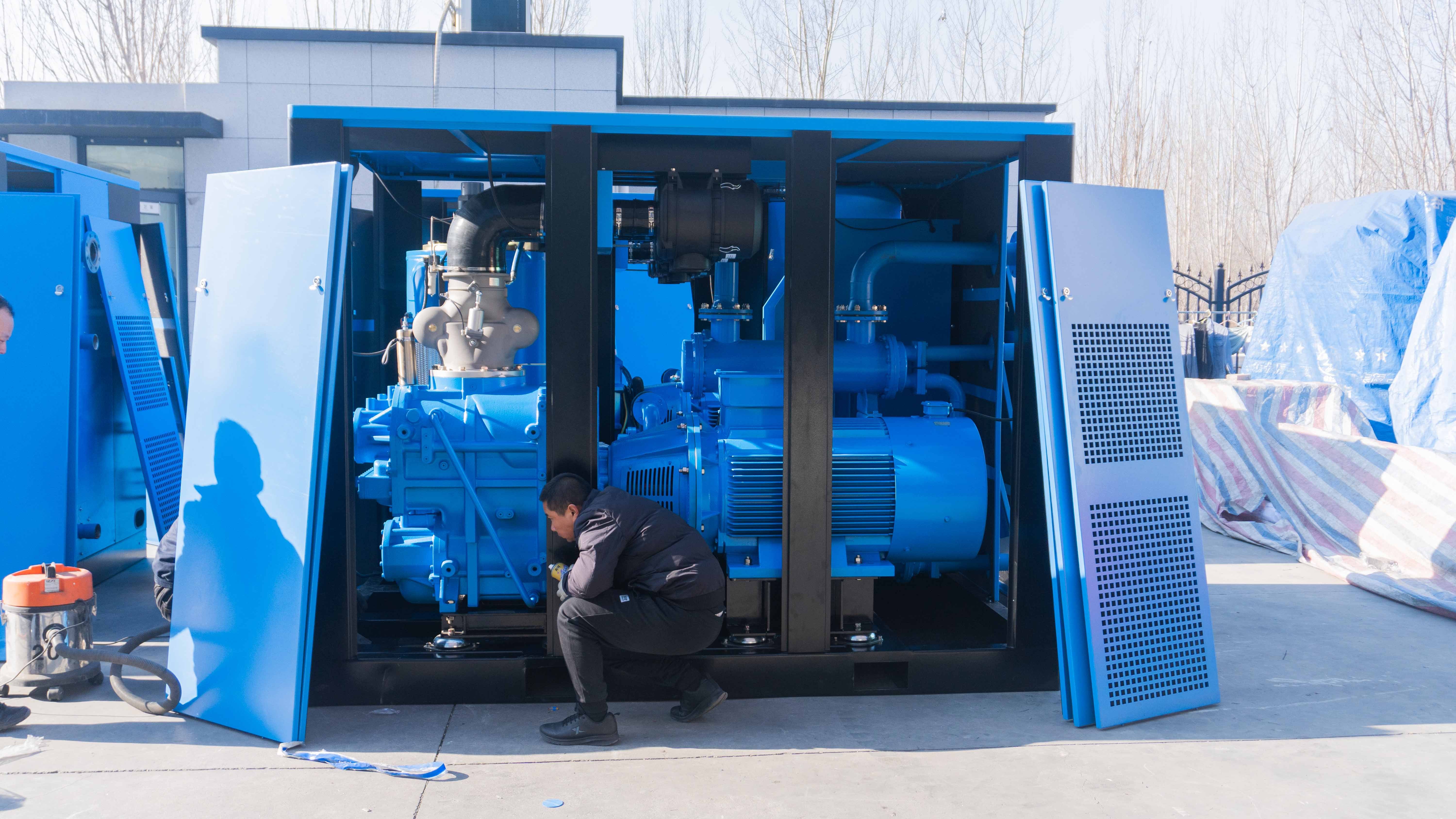

1. Introduction
The Importance of Large Chillers
Large chillers are critical components in HVAC (Heating, Ventilation, and Air Conditioning) systems, especially in commercial and industrial applications. They play a pivotal role in regulating indoor climates, preserving perishable goods, and cooling manufacturing processes. Chillers work by removing heat from a liquid via a vapor-compression or absorption refrigeration cycle. Among the key components of a chiller, the **compressor** is the heart of the system. It compresses the refrigerant, increasing its pressure and temperature, thereby enabling it to move through the refrigeration cycle and achieve the desired cooling effect.
The Role of Compressors in Chillers
In large chiller systems, the **compressor** is responsible for maintaining the required cooling capacity and ensuring energy efficiency. Choosing the right type of compressor is crucial, as it directly impacts the **refrigeration efficiency**, **energy consumption**, and **maintenance costs**. This article will provide a comprehensive overview of the different types of compressors used in large chillers, focusing on their operating principles, benefits, limitations, and suitability for various applications.
2. Overview of Common Compressor Types Used in Large Chillers
Large chillers typically use one of the following four types of compressors: **centrifugal compressors**, **screw compressors**, **reciprocating compressors**, and **scroll compressors**. Each type has unique characteristics that make it suitable for specific applications.
Centrifugal Compressors
**Centrifugal compressors** are widely regarded as the most efficient type for large chillers, especially in applications requiring high cooling capacities. They operate using centrifugal force to compress refrigerant gas. Centrifugal compressors are known for their **high efficiency**, **compact size**, and **low maintenance requirements**.
Screw Compressors
Screw compressors are another popular choice for large chillers, especially in medium to large applications. They use two intermeshing helical rotors to compress the refrigerant. These compressors are reliable, have fewer moving parts, and provide a **steady flow of refrigerant**.
Reciprocating Compressors
Reciprocating compressors use pistons driven by a crankshaft to compress refrigerant gas. Although less common in large chillers due to their lower efficiency and higher maintenance requirements, they are sometimes used in applications where precise control over capacity is needed.
Scroll Compressors
Scroll compressors use two interleaving spiral-shaped scrolls to compress refrigerant. They are more common in small to medium-sized chillers but can be used in large systems where space and noise are a concern.
3. Centrifugal Compressors: The Preferred Choice for Large Chillers
Working Principle
Centrifugal compressors work by converting kinetic energy into pressure. A rotating impeller accelerates the refrigerant gas, and this kinetic energy is converted into pressure energy as the gas flows through a diffuser. The process is highly efficient for high-capacity applications, making centrifugal compressors ideal for **large chillers**.
- Example: A 1,000-ton chiller with a centrifugal compressor can achieve a coefficient of performance (COP) of 6.5 to 7.0, making it highly efficient compared to other compressor types.
Advantages and Features
- High Efficiency: Centrifugal compressors can handle large volumes of refrigerant, making them highly efficient for large-capacity chillers. They are commonly used in **industrial refrigeration** and **large commercial HVAC systems**.
- Compact Design: These compressors have a relatively small footprint compared to their cooling capacity, which is beneficial in applications where space is limited.
- Low Maintenance: With fewer moving parts than reciprocating compressors, centrifugal compressors require less maintenance, resulting in lower long-term operational costs.
- Variable Speed Drive (VSD) Compatibility: VSD technology can be integrated to optimize energy use, further enhancing the energy efficiency of centrifugal compressors.
Suitable Applications
Centrifugal compressors are the go-to choice for large-scale cooling needs, such as:
- Data Centers: Where continuous, reliable cooling is essential.
- Hospitals: Where HVAC systems need to operate efficiently around the clock.
- Large Commercial Buildings: Including malls and office complexes, where energy consumption is a significant concern.
4. Application of Other Compressor Types in Large Chillers
Screw Compressors: Advantages and Limitations
Screw compressors are used in applications requiring medium to large cooling capacities. They are known for their reliability, moderate efficiency, and ability to handle fluctuating loads.
- Advantages:
- Consistent Cooling: Screw compressors provide a constant flow of refrigerant, making them suitable for applications where a steady cooling load is required.
- Less Vibration and Noise: Compared to reciprocating compressors, screw compressors operate more quietly and with less vibration, which is beneficial in environments where noise is a concern.
- Lower Maintenance: With fewer parts and less friction, screw compressors generally require less maintenance.
- Limitations:
- Lower Efficiency: Compared to centrifugal compressors, screw compressors are less efficient in high-capacity applications.
- Higher Initial Costs: The upfront cost of screw compressors can be higher due to their design and technology.
Reciprocating and Scroll Compressors: Application Scope
Reciprocating compressors are generally used in smaller chiller systems or where specific conditions make them suitable, such as in systems requiring precise capacity control.
- Advantages:
- Precise Capacity Control: The ability to control capacity in small increments is ideal for applications with varying load requirements.
- Limitations:
- High Maintenance Requirements: Due to the many moving parts, reciprocating compressors often have higher maintenance needs and shorter service life compared to other types.
Scroll compressors are not typically used in large chillers but can be effective in smaller systems or in cases where quiet operation and compact size are essential.
- Advantages:
- Quiet Operation: Minimal noise makes scroll compressors suitable for environments where noise reduction is crucial.
- Compact Design: Scroll compressors have a small footprint, making them ideal for tight installations.
- Limitations:
- Limited Capacity: Not suitable for high-capacity applications like large chillers.
5. Considerations for Choosing the Type of Compressor
When selecting a compressor for a large chiller, several factors must be considered:
Cooling Capacity Requirements
- For chillers requiring high cooling capacities (above 500 tons), centrifugal compressors are usually the most efficient choice.
- For medium-capacity needs (100-500 tons), screw compressors may offer a balance between efficiency and cost.
Energy Efficiency Requirements
- Centrifugal compressors offer the highest **energy efficiency** for large-scale applications, especially when combined with VSD technology.
- Screw compressors provide moderate energy efficiency and can be suitable for variable load applications.
Operating Costs
- The initial cost of centrifugal compressors may be higher, but their lower maintenance and operational costs often result in lower total cost of ownership.
- Reciprocating compressors tend to have higher maintenance costs, which can offset their lower initial purchase price.
Maintenance Considerations
- Centrifugal and screw compressors require less frequent maintenance compared to reciprocating compressors, resulting in reduced downtime and lower maintenance costs.
6. Future Trends
Technological Innovations
- Magnetic Bearing Compressors: Emerging technology in centrifugal compressors, offering even greater efficiency and reduced maintenance.
- Oil-Free Compressors: Growing in popularity due to environmental and efficiency benefits, particularly in **HVAC systems** and industrial refrigeration.
Environmental Regulations Impacting Compressor Selection
- With increasing environmental regulations on refrigerants and energy efficiency, the choice of compressors in large chillers is shifting towards more sustainable and eco-friendly options.
7. Conclusion
In conclusion, **centrifugal compressors** are the most often used type of compressor in large chillers due to their high efficiency, compact design, and lower maintenance needs. While other compressor types like **screw**, **reciprocating**, and **scroll compressors** have their applications, centrifugal compressors offer the best balance of performance, efficiency, and cost for large-scale cooling needs. The choice of the right compressor depends on several factors, including cooling capacity requirements, energy efficiency, operational costs, and maintenance needs. With technological advancements and evolving environmental standards, the future of compressors in large chillers will likely see further innovations focused on sustainability and efficiency.
1. The original airend is sourced directly from Germany, ensuring top-notch engineering and quality.
2. The air produced is 100% oil-free and is certified by the renowned German organization TUV, ensuring the highest standards of purity.
3. Equipped with a centrifugal fan, this system offers a superior cooling effect, maintaining optimal performance and efficiency.
1. The original airend is sourced directly from Germany, ensuring top-notch engineering and quality.
2. The air produced is 100% oil-free and is certified by the renowned German organization TUV, ensuring the highest standards of purity.
3. Equipped with a centrifugal fan, this system offers a superior cooling effect, maintaining optimal performance and efficiency.
75 KW 100 HP Mobile Diesel Rotary Screw Truck Air Compressor 100 cfm 7/8/10/13 Bar Equipment Leasing
1. Compact and portable: The compact and portable design of the Jinjing brand diesel rotary screw air compressor for truck make
Jinjing brand reciprocating piston high pressure air compressors are widely used in precision machinery